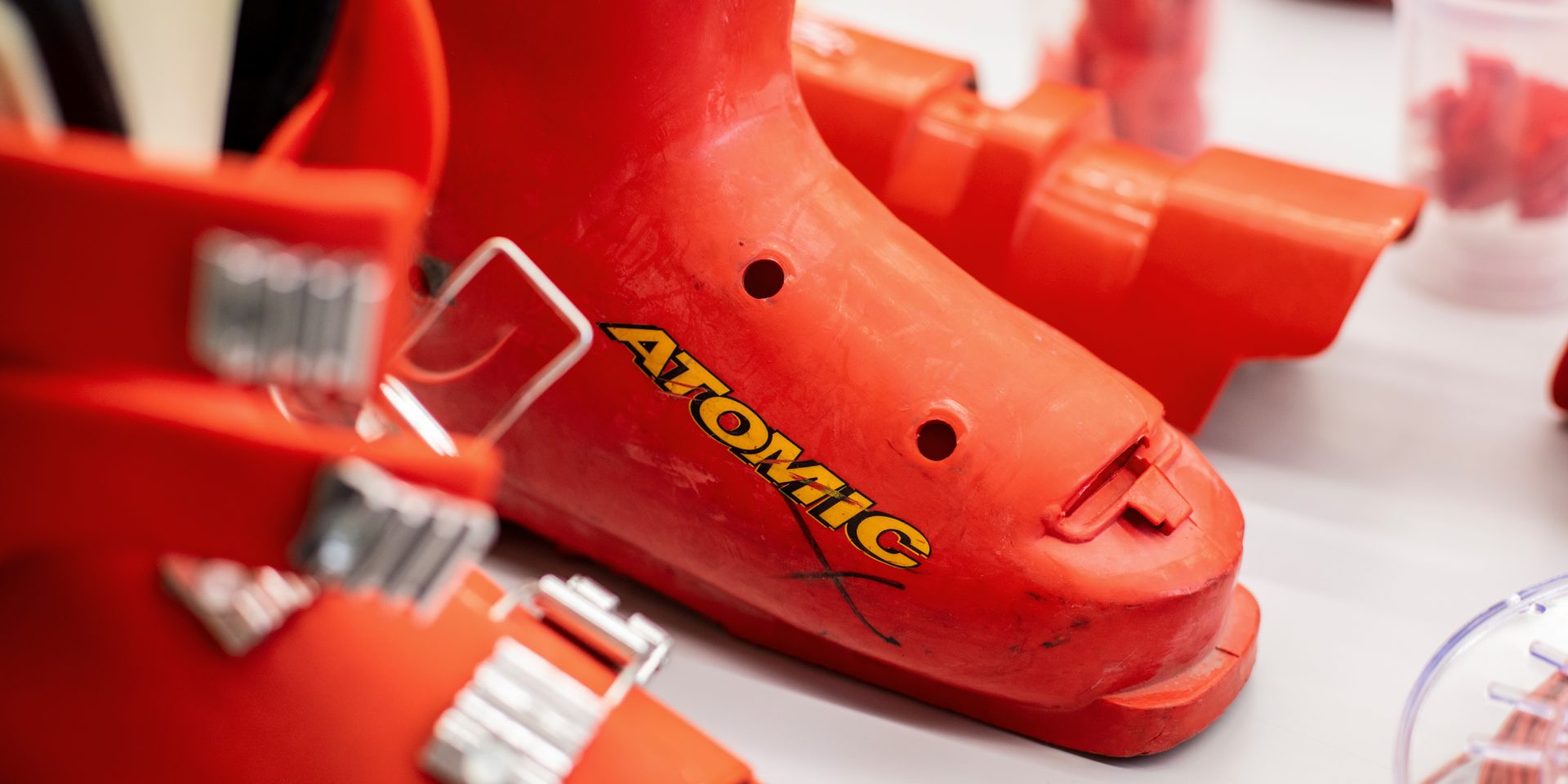
Upcycling und 3D-Druck – Symbiose für die Kreislaufwirtschaft?
Auf einem Tisch steht ein roter Skischuh. Den intensiven Gebrauch aus vergangenen Wintern sieht man ihm gut an. Dem aktuellen Zeitgeschmack entspricht er auch nicht mehr so ganz. Selbst in einem Secondhandladen würde er wohl schwer noch einen Käufer finden. Was also mit ihm machen? Wegwerfen? Daniel Schwendemann ist anderer Meinung. Für ihn steht auf dem Tisch ein Rohstoff, der sich besonders gut für die Produktion von Maschinenteilen, Gussformen oder Luftfiltergehäusen eignet.
Es ist denn auch kein Zufall, dass der rote Skischuh seinen Weg ins Laboratorium des Instituts für Werkstofftechnik und Kunststoffverarbeitung (IWK) der Hochschule Rapperswil (HSR) gefunden hat. In Zusammenarbeit mit der ARGO Werkstätte für Menschen mit Behinderung in Davos haben Schwendemann, stellvertretender Institutsleiter und Professor am IWK, und sein Team ein elastisches Filament entwickelt, das zu 100% aus solchen Skischuhen hergestellt wird. Gedacht ist es für den Einsatz in 3D-Druckern.
Weltweit ist das ein Novum. Die wiederverwendeten Skischuhe werfen ein Licht auf den 3D-Druck, dessen digitaler Technologie attestiert wird, dass sie das Konzept der Kreislaufwirtschaft entscheidend unterstützen kann. Der Einsatz von Upcycling-Kunststoff im 3D-Druck entspricht dabei einer kreislaufwirtschaftlichen Konsequenz. Nicht zuletzt geht es auch darum, die Kreislaufwirtschaft als Geschäftsmodell zu nutzen.
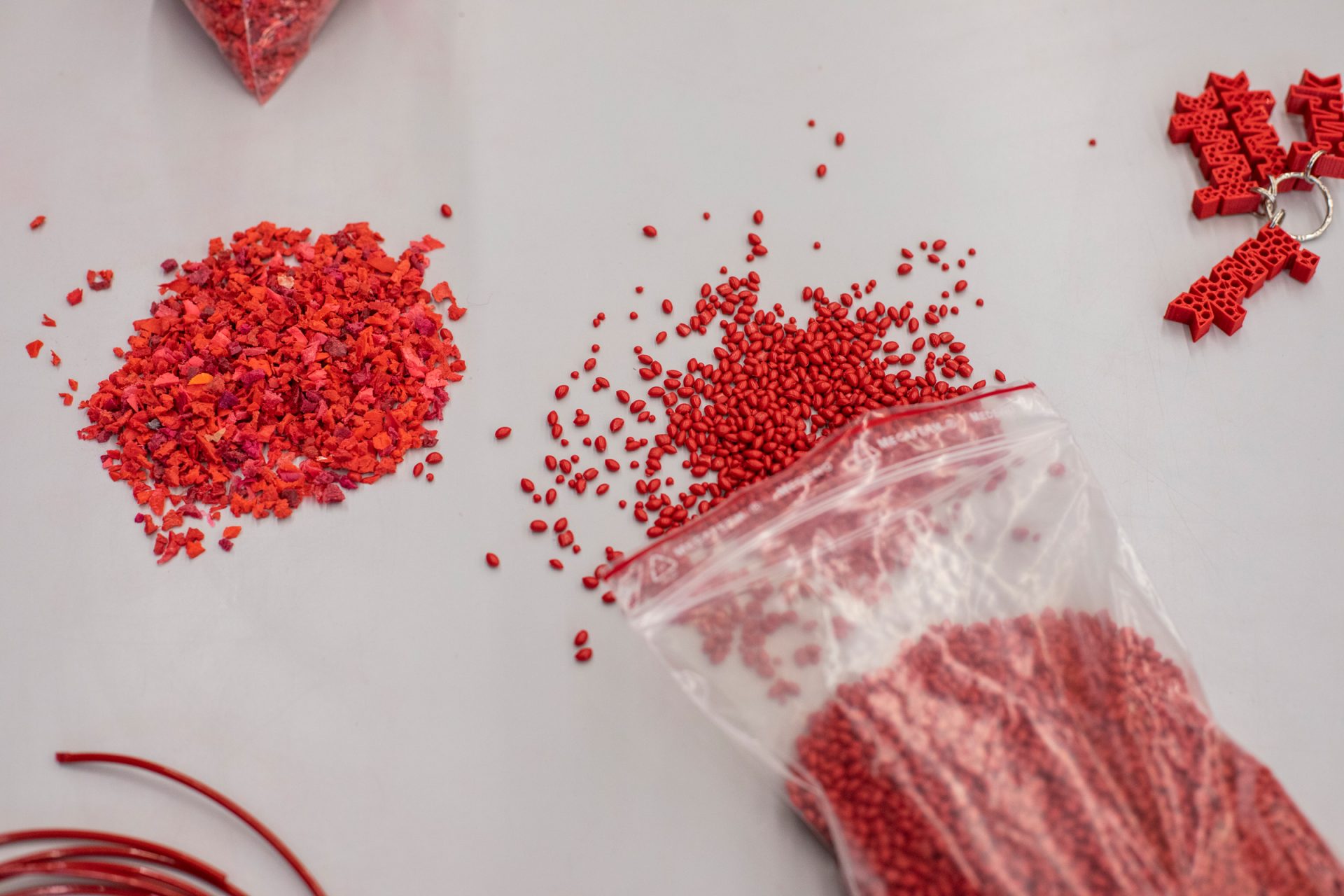
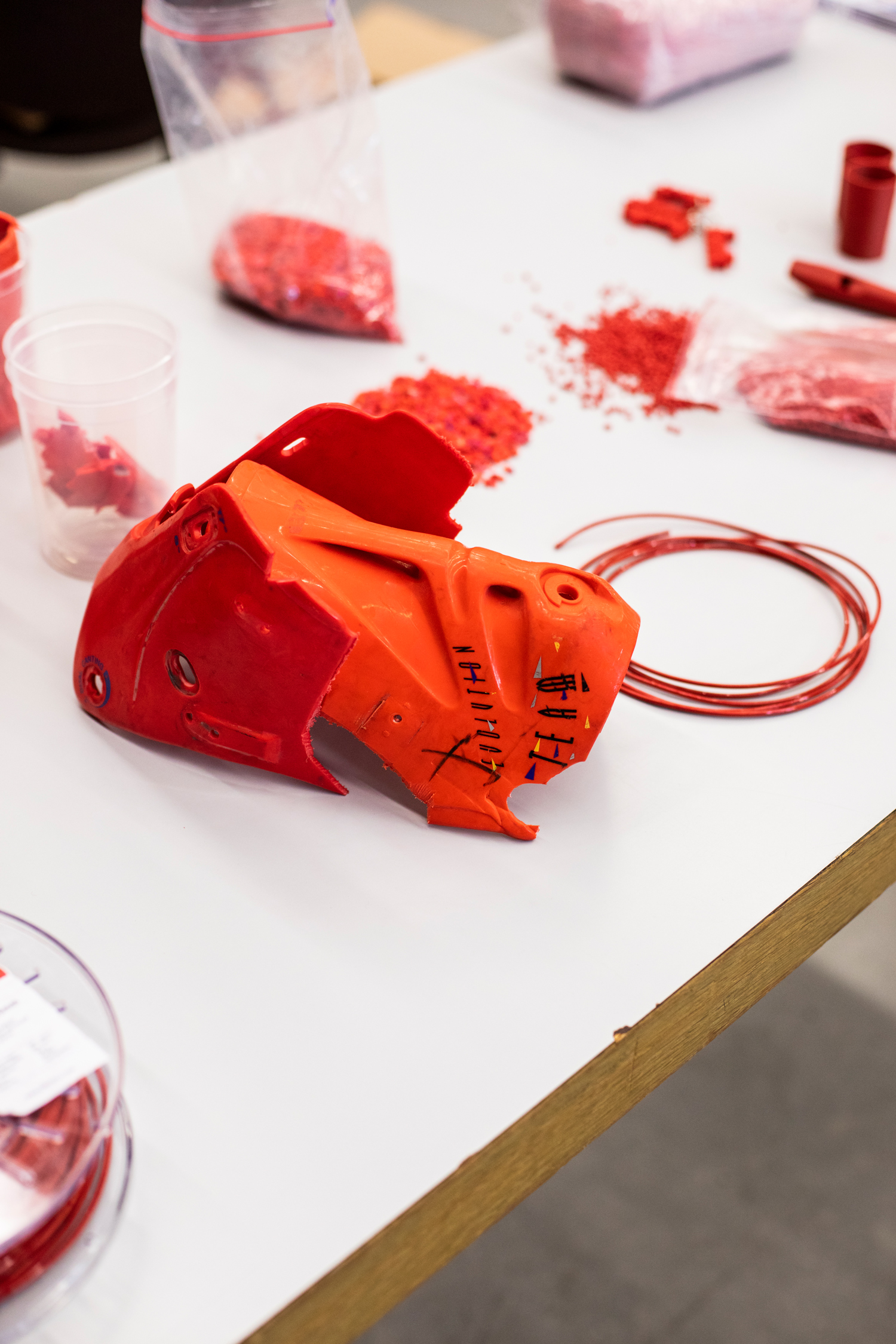
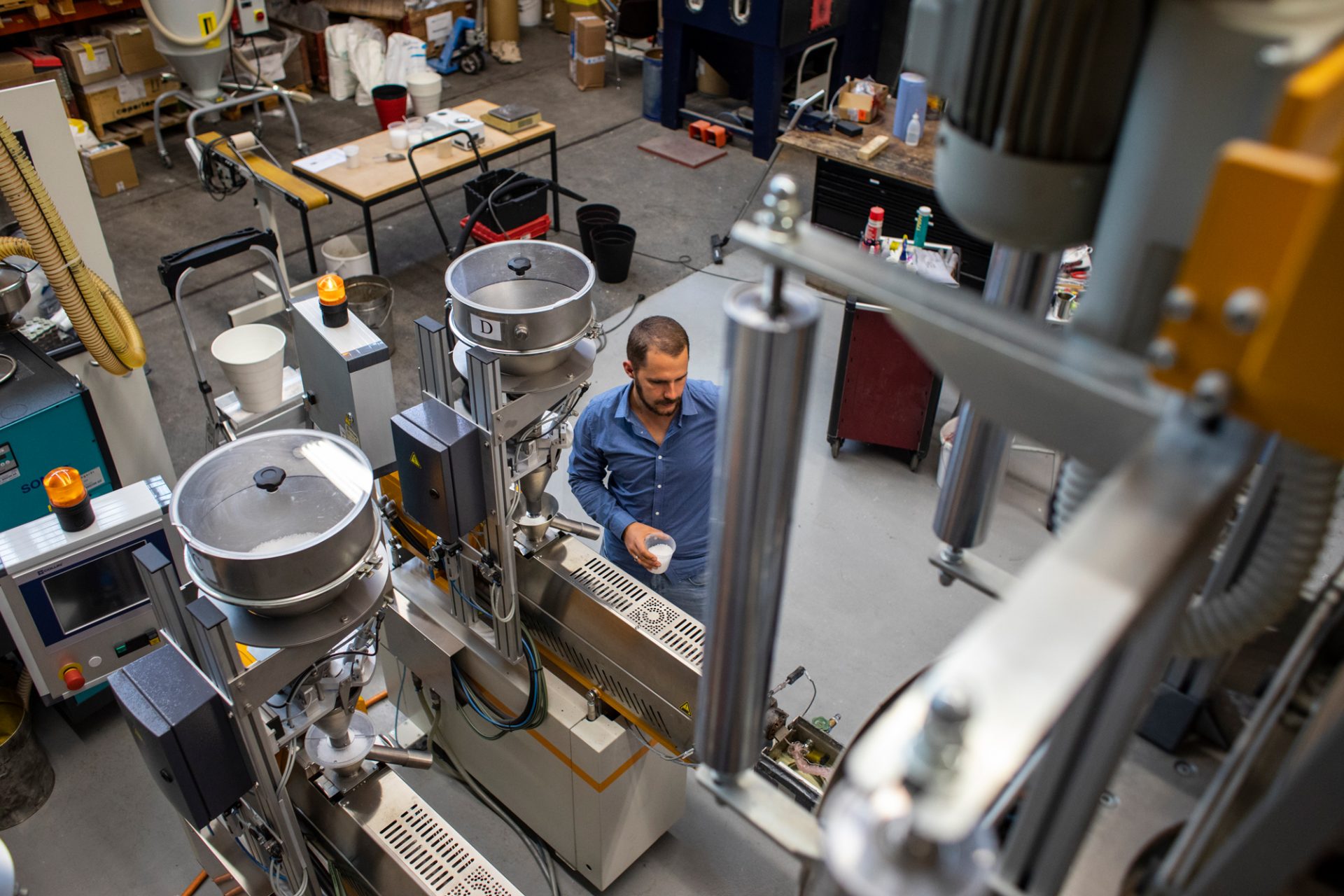
3D-Druck und Upcycling
Im Zusammenhang mit dem Konzept der Kreislaufwirtschaft wird die Digitalisierung in jüngerer Vergangenheit immer stärker diskutiert. Ansätze wie die Sensorik, das IoT, die Blockchain-Technologie oder auch derjenige der künstlichen Intelligenz stehen dabei meist im Vordergrund.
Als ein seit Kurzem öfters diskutierter Kandidat gilt auch der 3D-Druck. Dabei werden, in unterschiedlichen Verfahren, mithilfe von «Computer-Aided Design» (CAD) Materialien Schicht für Schicht aufgetragen und so dreidimensionale Objekte hergestellt. Was in den späten 1980er Jahren als wissenschaftliche Spielerei begann, ist heute in den Konstruktionsabteilungen vieler Unternehmen zum fest etablierten Hilfsmittel in der Herstellung von Modellen, Ersatzteilen und Bauelementen geworden.
«Früher sprach man vom sogenannten ‹Rapid Prototyping› und heute vom ‹Additive Manufacturing›», meint Schwendemann. Bereits anhand dieser begrifflichen Änderung erkennt man den Bedeutungswandel, den der 3D-Druck erfahren hat.
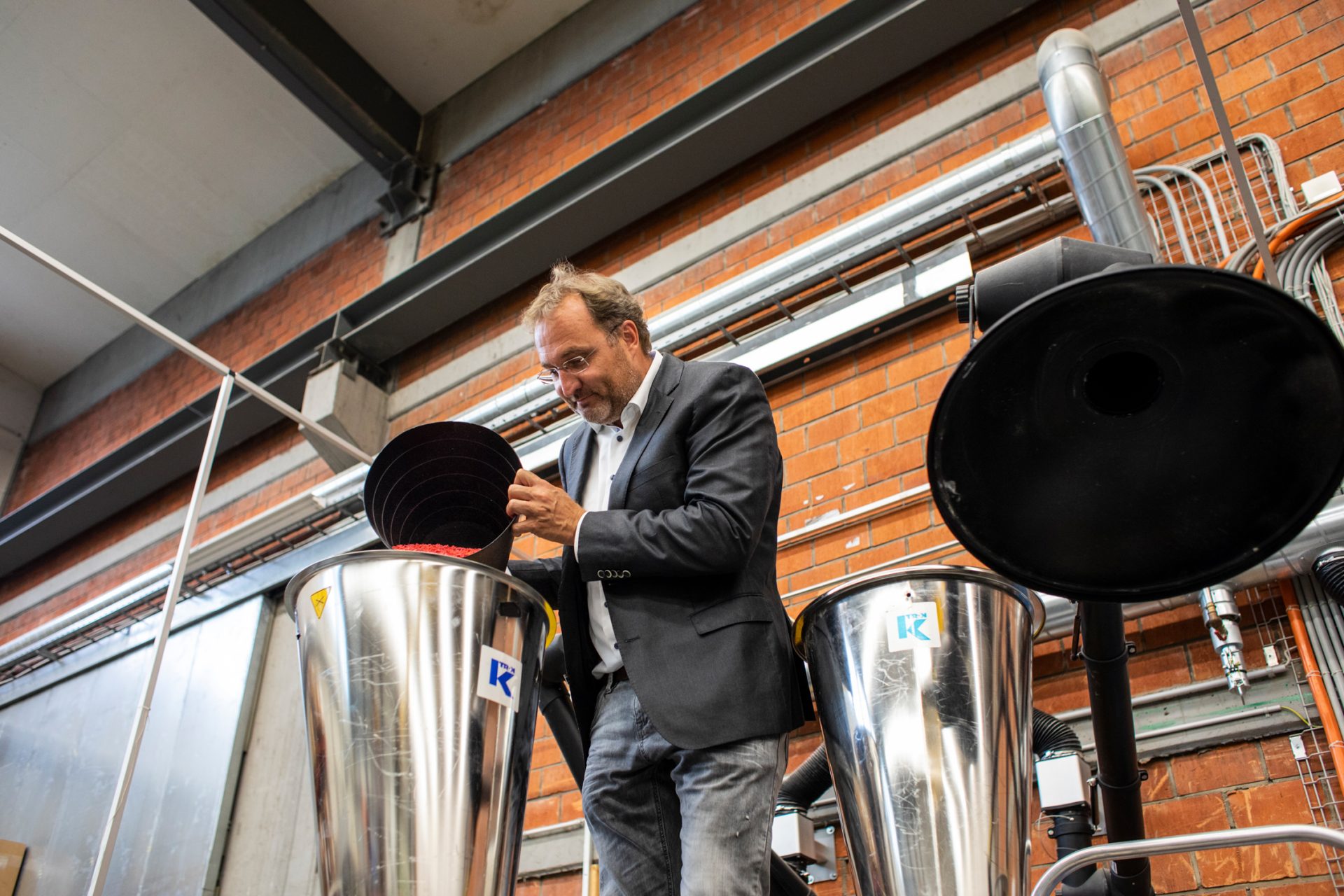
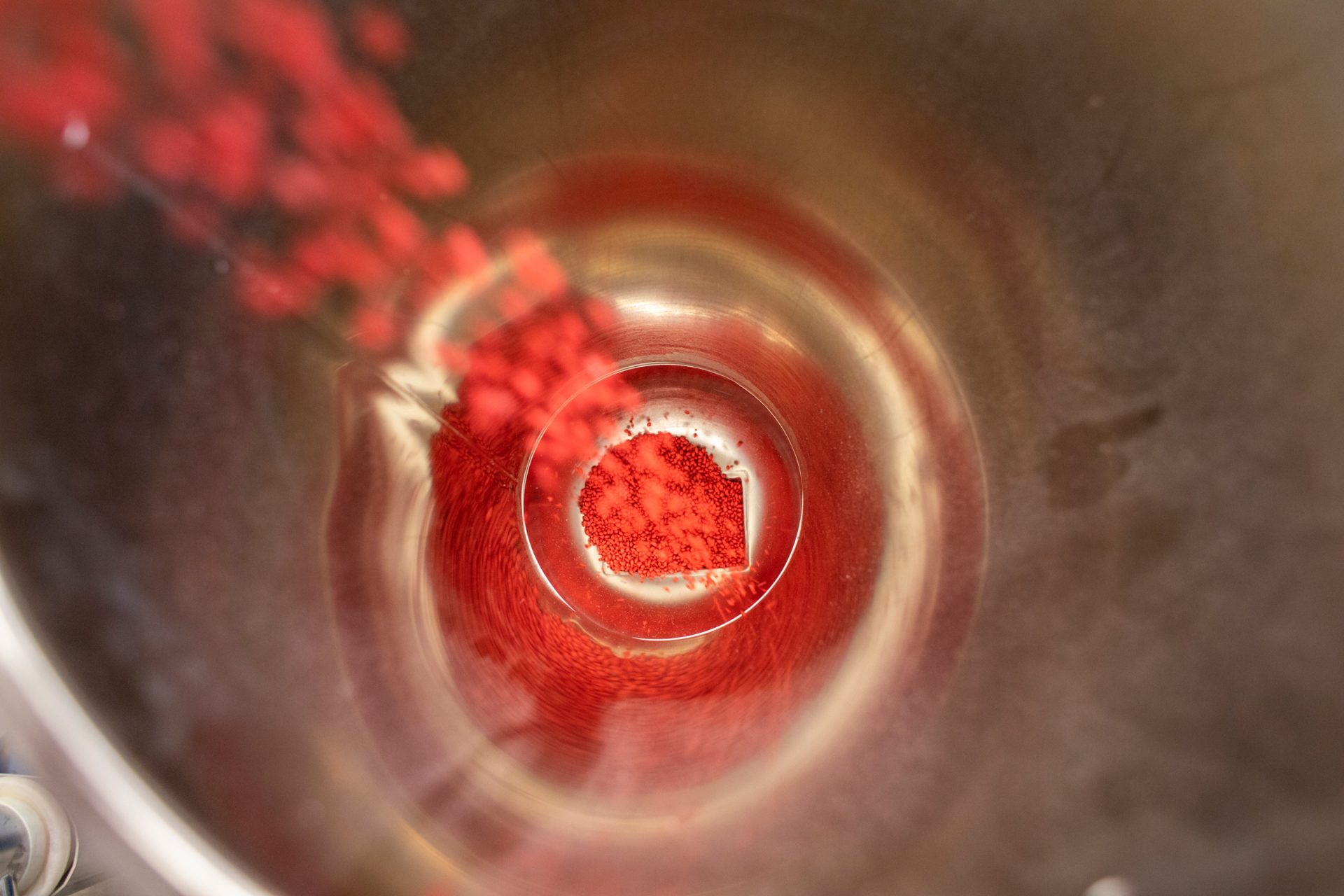
2018 wies eine Studie des deutschen Umweltbundesamts (UBA) auf die Chancen des 3D-Drucks für die Kreislaufwirtschaft hin. Gerade im Bereich von komplexen Leichtbaukonstruktionen für die Bau-, Automobil- oder die Flugzeugindustrie verortet die Studie erhebliches Potenzial zur Verminderung des Ausstosses von Treibhausgasen.
Besonders Sinn machen 3D-Drucker gemäss den Verfassern der Studie aber gerade auch dann, wenn es darum geht, neue Recyclingkonzepte zu erschliessen. So können für den Betrieb von 3D-Druckern beispielsweise Kunststoffabfälle zur Produktion von neuen Produkten verwendet werden. In solchen Fällen spricht man dann von einer ganz spezifischen Variante des Recyclings. Dem sogenannten «Upcycling». Vom klassischen Recycling hebt es sich dadurch ab, dass die bei diesem Prozess hergestellten neuen Produkte von gleichwertiger oder besserer Qualität als das Ursprungsprodukt sind.
Upcycling-Projekte für den 3D-Druck sind keine Zukunftsmusik mehr. So sammelt beispielsweise das Designstudio The New Raw aus Rotterdam alte Fischernetze und produziert damit im 3D-Drucker Vasen und Schalen. Ein anderes Beispiel stellt die Non-Profit-Organisation Kindness3D aus dem kanadischen Halifax dar, die Kunststoffdeckel sammelt und daraus kostengünstige Prothesen druckt. Sogar in übersphärische Dimensionen hat es die Idee bereits geschafft. Und das im wortwörtlichen Sinn. So druckt die NASA mit ihrem Refabricator auf der ISS aus Kunststoffabfall Werkzeuge für ihre Astronauten.
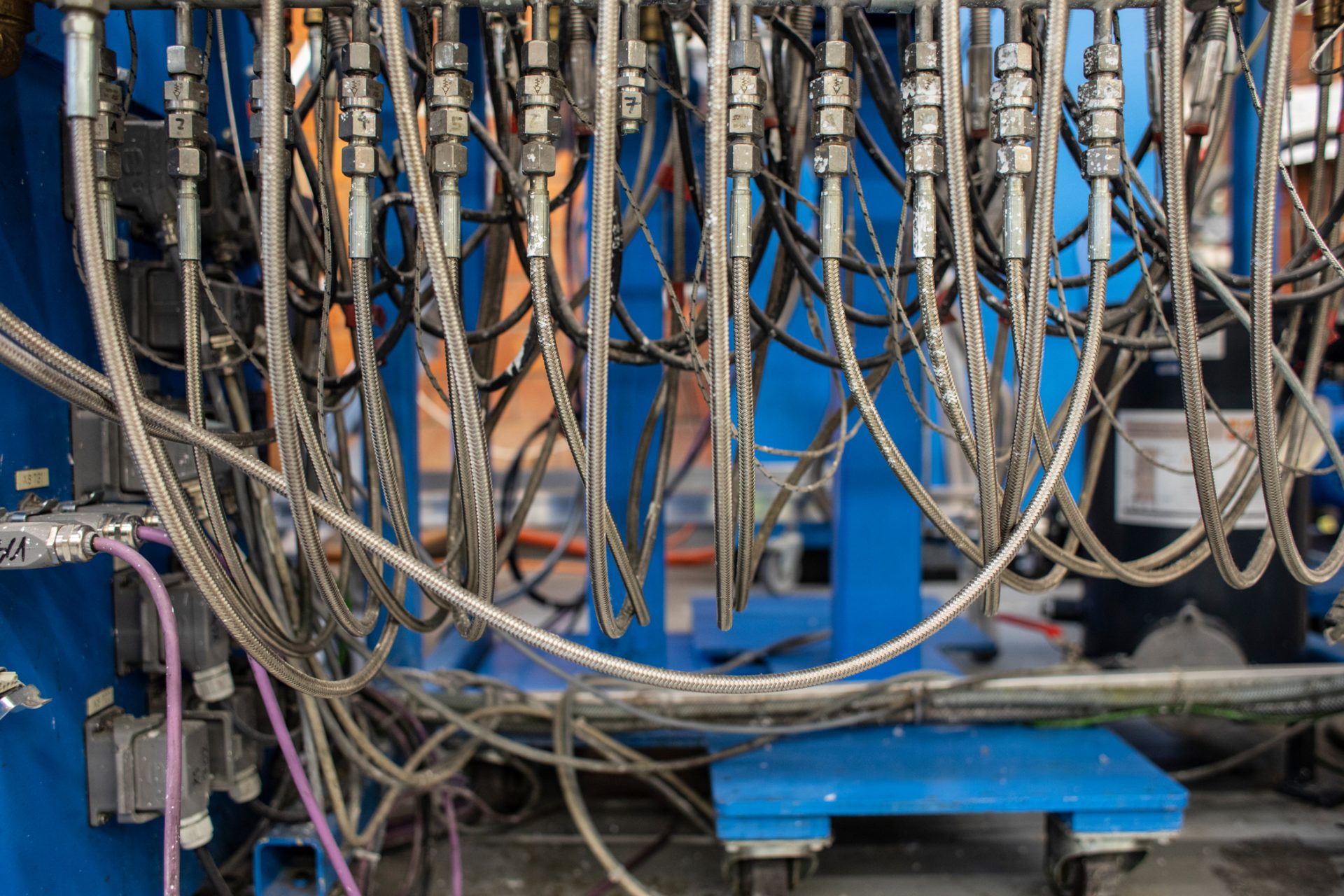
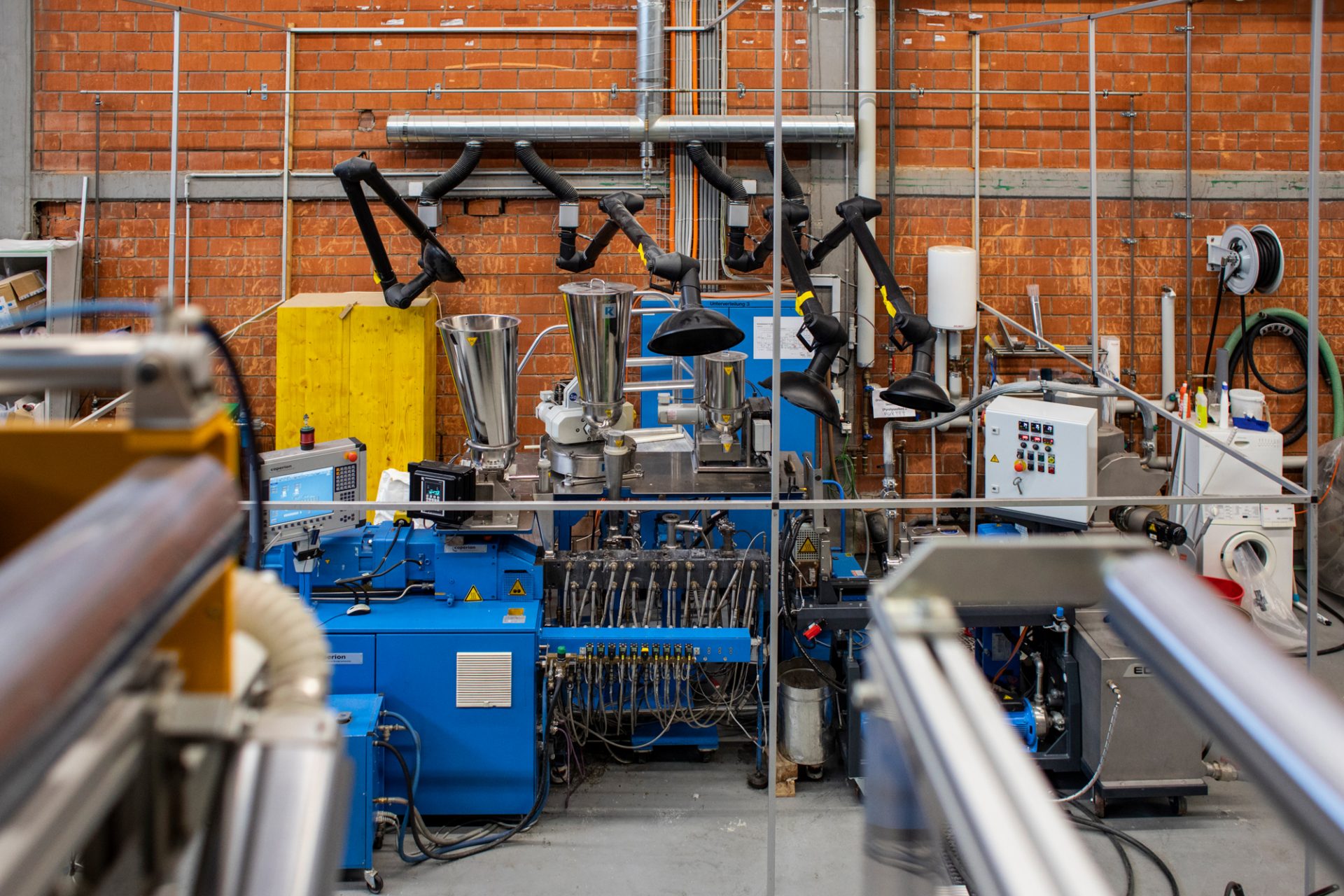
Eine Plattenpresse geht kaputt
Eines der ersten Beispiele für das Upcycling von Kunststoff für den Einsatz in 3D-Druckern war das Filament CREAMELT® TPU-R des IWK. Die Idee dazu entstand bereits 2012. Damals trat die ARGO Werkstätte in Davos an das IWK mit der Fragestellung nach einer neuen Anwendungsmöglichkeit für ihr Recyclingmaterial heran. Rund 8000 Skischuhe wurden bis dahin in der ARGO Werkstätte jedes Jahr gesammelt, nach Farben sortiert und in Handarbeit zerlegt. Daraus wurden Bodenplatten gepresst, die beispielsweise an Skiliftanlagen verlegt wurden.
«Ein Totalausfall der Plattenpresse und neue Brandschutzbestimmungen führten dazu, dass dies nicht mehr ging und man eine Alternative suchen musste», so Schwendemann. «Gerade in dieser Zeit erlebte auch die 3D-Druck-Technologie eine immer stärkere Verbreitung. Das hing damit zusammen, dass damals wichtige Patente für die Technologie ausliefen und die Kosten dafür innert kurzer Zeit stark sanken.»
Aufgrund dieser Ausgangslage entstand die Idee, aus den Skischuhen Druckmaterial für 3D-Drucker, sogenannte Filamente, herzustellen. «Mit unserem Projekt wollten wir aufzeigen, was im Bereich des Kunststoffrecyclings grundsätzlich möglich ist. Nämlich, dass man mit einem intelligenten Recycling ein neues, hochwertiges und ganz spezifisches Produkt im kreislaufwirtschaftlichen Sinn herstellen kann.»
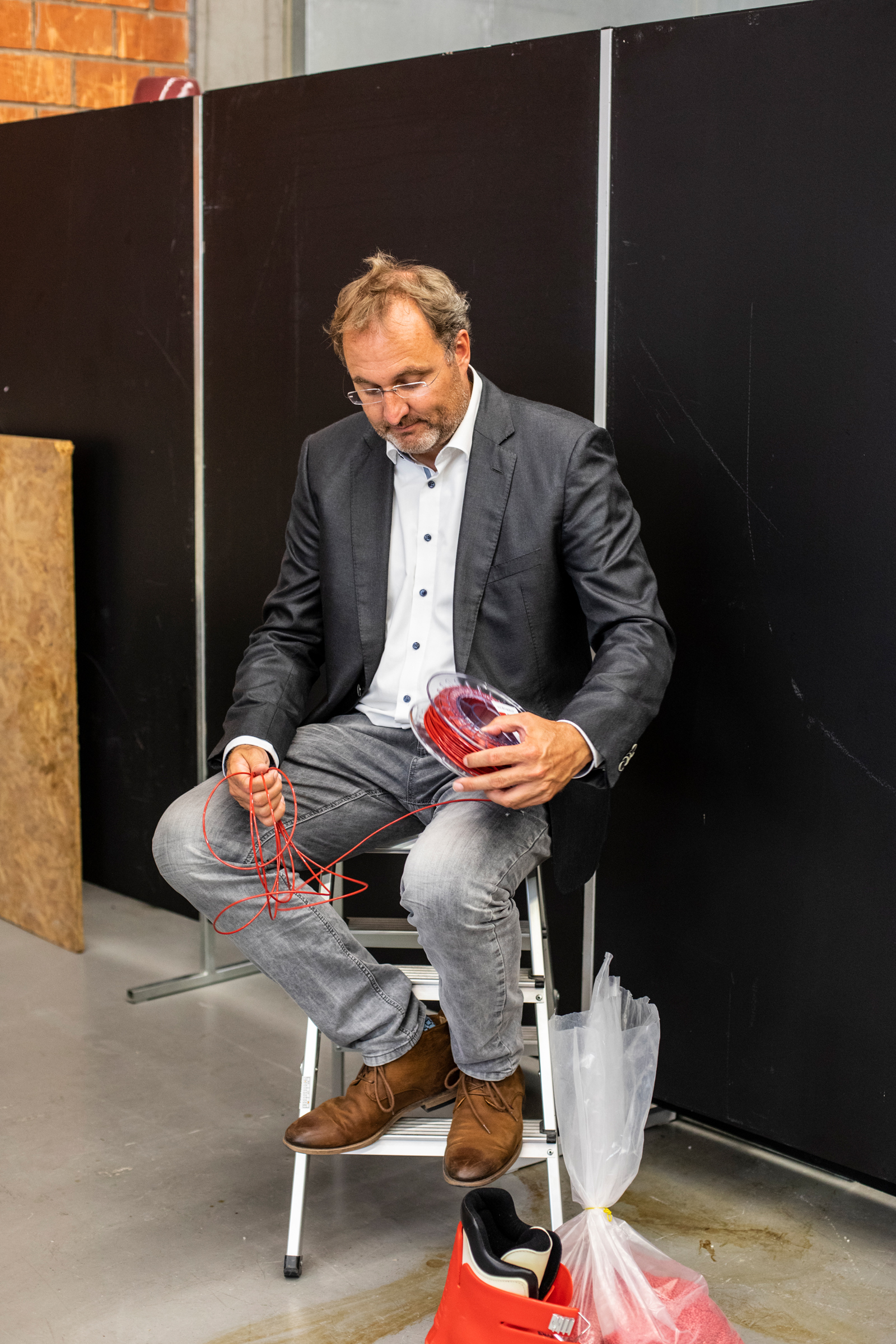
Dank lokaler Wertschöpfung vom Skischuh zum Filament
Vom Skischuh bis zum fertigen Filament für den 3D-Drucker war es ein weiter Weg. Wurden die Skischuhe in der ARGO Werkstätte für ihre anfängliche Verwendung noch ausschliesslich nach Farben sortiert, so stand beim IWK zunächst die Identifikation der für die Schuhe verwendeten Kunststoffe im Fokus. «Nach ausführlichen analytischen Untersuchungen konnten wir feststellen, dass Skischuhe aus ganz unterschiedlichen Materialien bestehen. Zu rund 50% bestehen sie aber aus dem elastischen und kälteschlagzähen Elastomer Polyurethan (TPU)», so Schwendemann.
Um eine möglichst hohe Materialqualität dieses Sekundärrohstoffs zu erzielen, stellte sich die Frage, wie das vorhandene Material identifiziert werden sollte. Sprich, welche Teile der Skischuhe aus dem gewünschten TPU bestehen. Im Rahmen einer Bachelorarbeit eines Studenten entstand das entsprechende Handwerkszeug dazu.
«Mithilfe eines bestimmten Trennverfahrens, welches das Absorptionsverhalten von Kunststoffen im Infrarotbereich misst und laufend mit einer Datenbank abgleicht, kann das gewünschte TPU von den Mitarbeitenden der ARGO heute bestimmt und sortenrein getrennt werden.» Alles was bis hierhin geschieht, findet in Davos statt. «Die weiteren Schritte auf dem Weg zum fertigen Filament finden bei uns im Kunstofftechnikum des IWK statt.»
Getrennt nach Farben, wird der Rohstoff hier zunächst gemahlen und dann in einem sogenannten Compounder weiterverarbeitet. «Dabei wird das Mahlgut geschmolzen, homogenisiert, entgast, gesiebt und mittels Unterwassergranulierung zu Granulat verarbeitet.» Für die abschliessende Verarbeitung des Granulats zu Filamenten entwickelte das IWK eine eigene Produktionslinie, in der das recycelte Granulat mit ganz spezifischen Rundheits- und Durchmessertoleranzen extrudiert wird. Gerade das ist für den optimalen Einsatz in 3D-Druckern entscheidend.
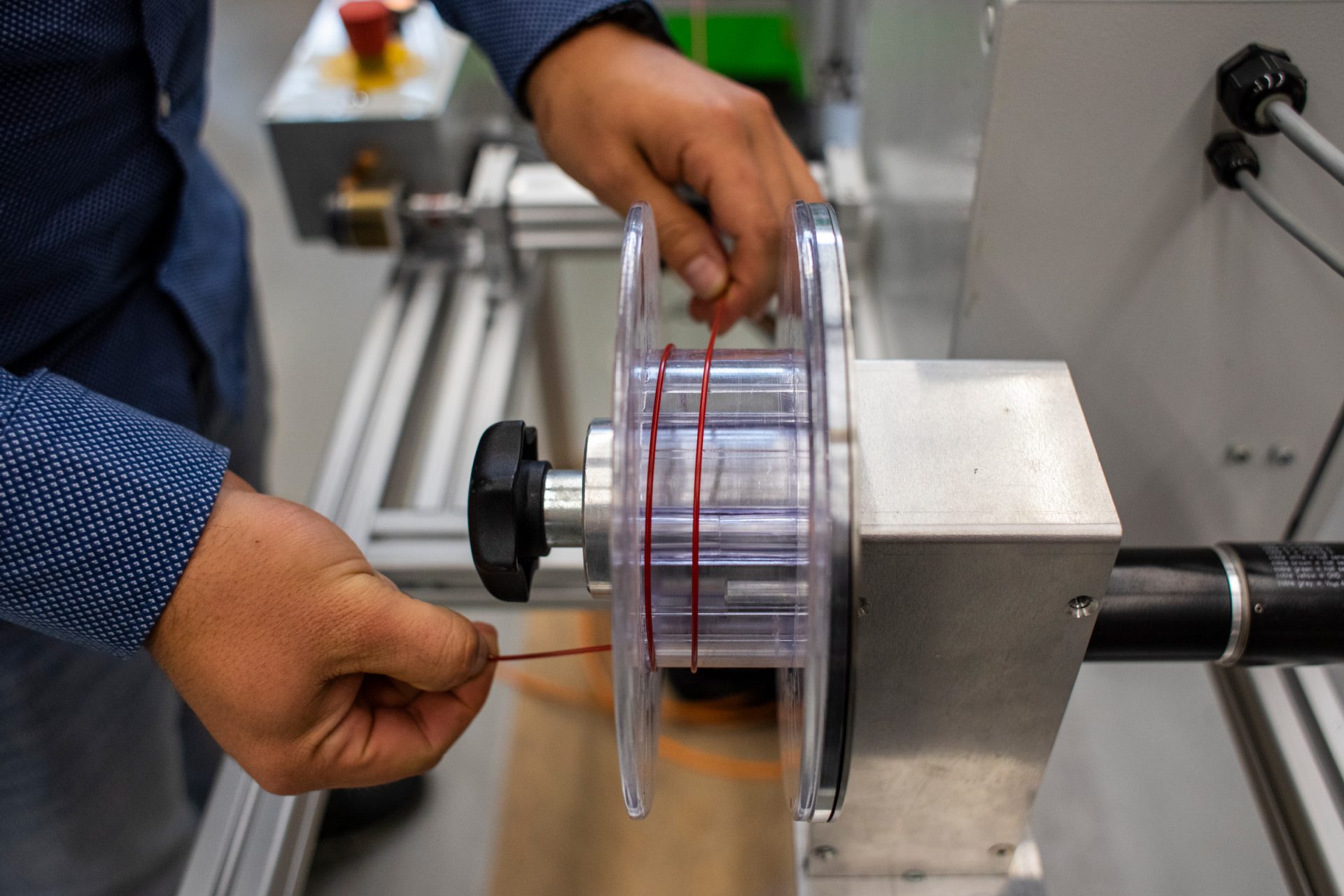
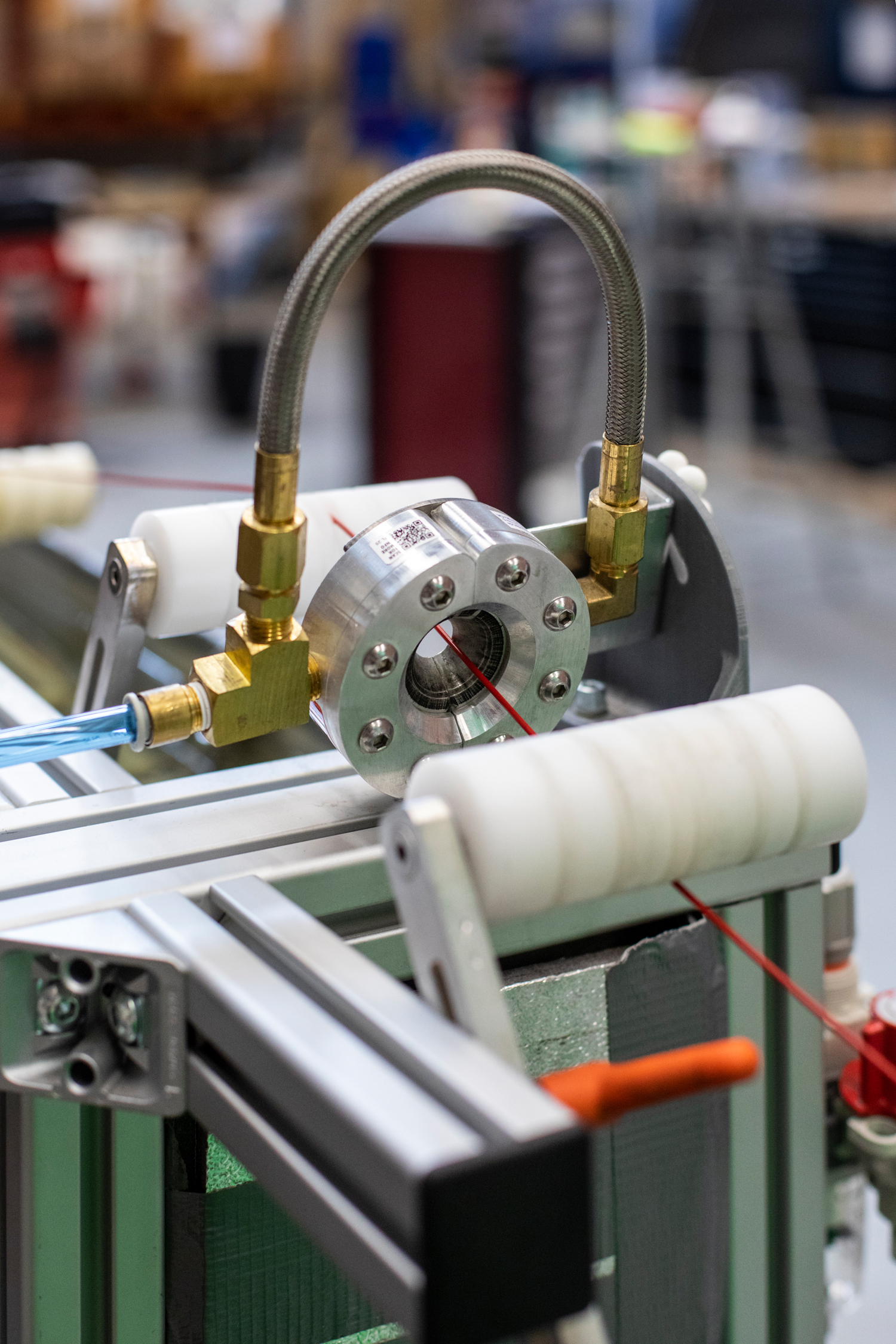
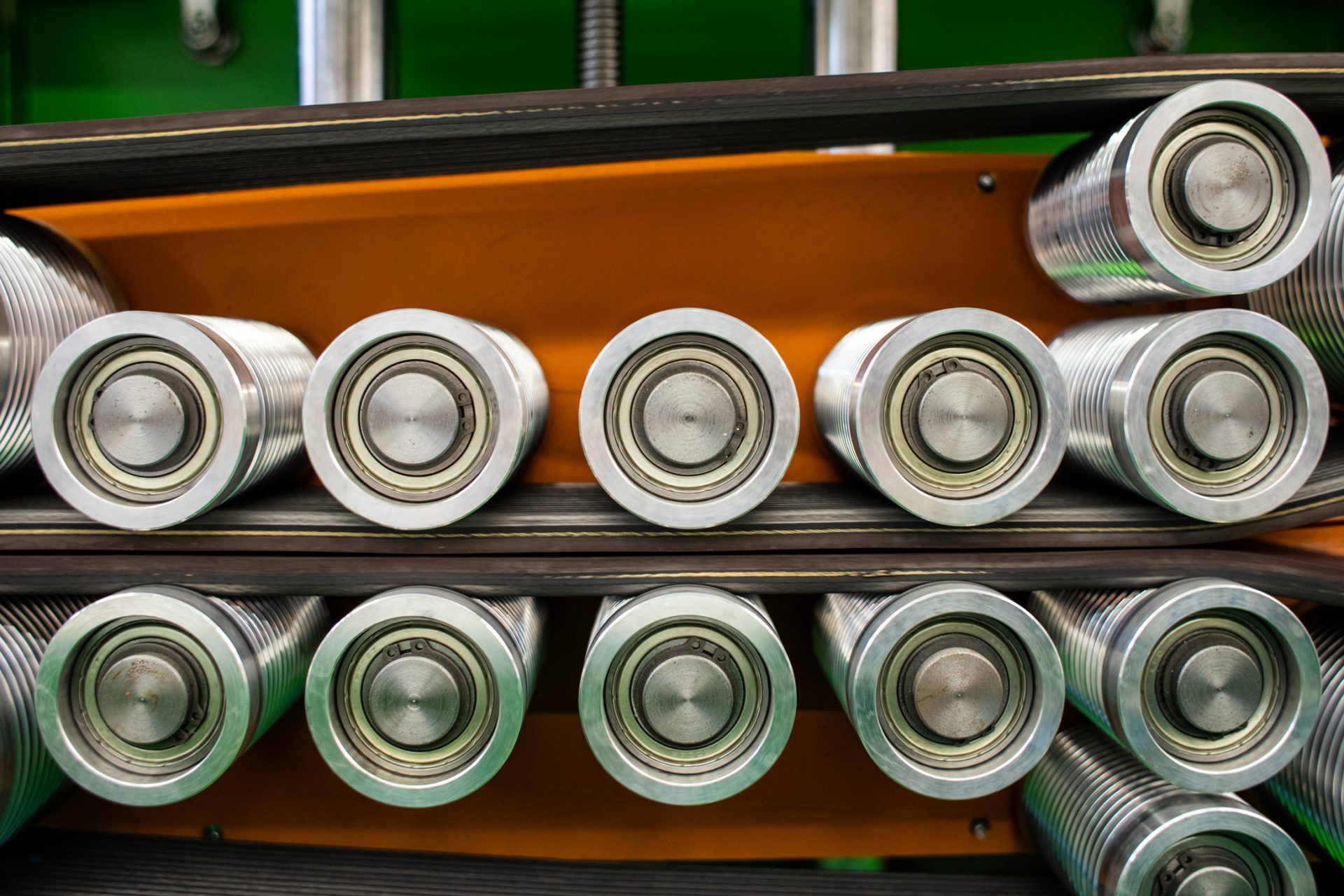
Spezifische Materialeigenschaften prädestinieren künftige Anwendungen
Die spezifischen Materialeigenschaften des neuen Filaments prädestinieren es für die Produktion von bestimmten Produkten im 3D-Druck. «Als wir begonnen haben, wurden für den 3D-Drucker noch hauptsächlich gängige Standardmaterialien verwendet, die nicht elastisch waren. Gerade daher gab es eine Nachfrage nach Alternativmaterialien, welche sich gut verarbeiten lassen und gleichzeitig auch belastbar sind.» Dass sich das in den Skischuhen verarbeitete TPU dafür besonders gut eignet, zeigte sich bereits bei den ersten Produktionstests.
Eigenschaften, die für Skischuhe wichtig sind, können hier zu anderen Zwecken genutzt werden. «So haben wir gute Resultate mit TPU-R erzielen können, beispielsweise beim Drucken von Luftfiltergehäusen oder aber auch von Schalungselementen für filigrane Betonkonstruktionen.» Damit kommt den ursprünglichen Materialeigenschaften des Rohstoffs für den 3D-Drucker im Rahmen des Upcyclings eine besondere Bedeutung zu. Wenn man diese kennt, rücken bestimmte Anwendungsmöglichkeiten bei der Produktion neuer Produkte noch stärker in den Vordergrund. Upcycling auf höchstem Niveau für einen digitalen Wegbereiter der Kreislaufwirtschaft also?
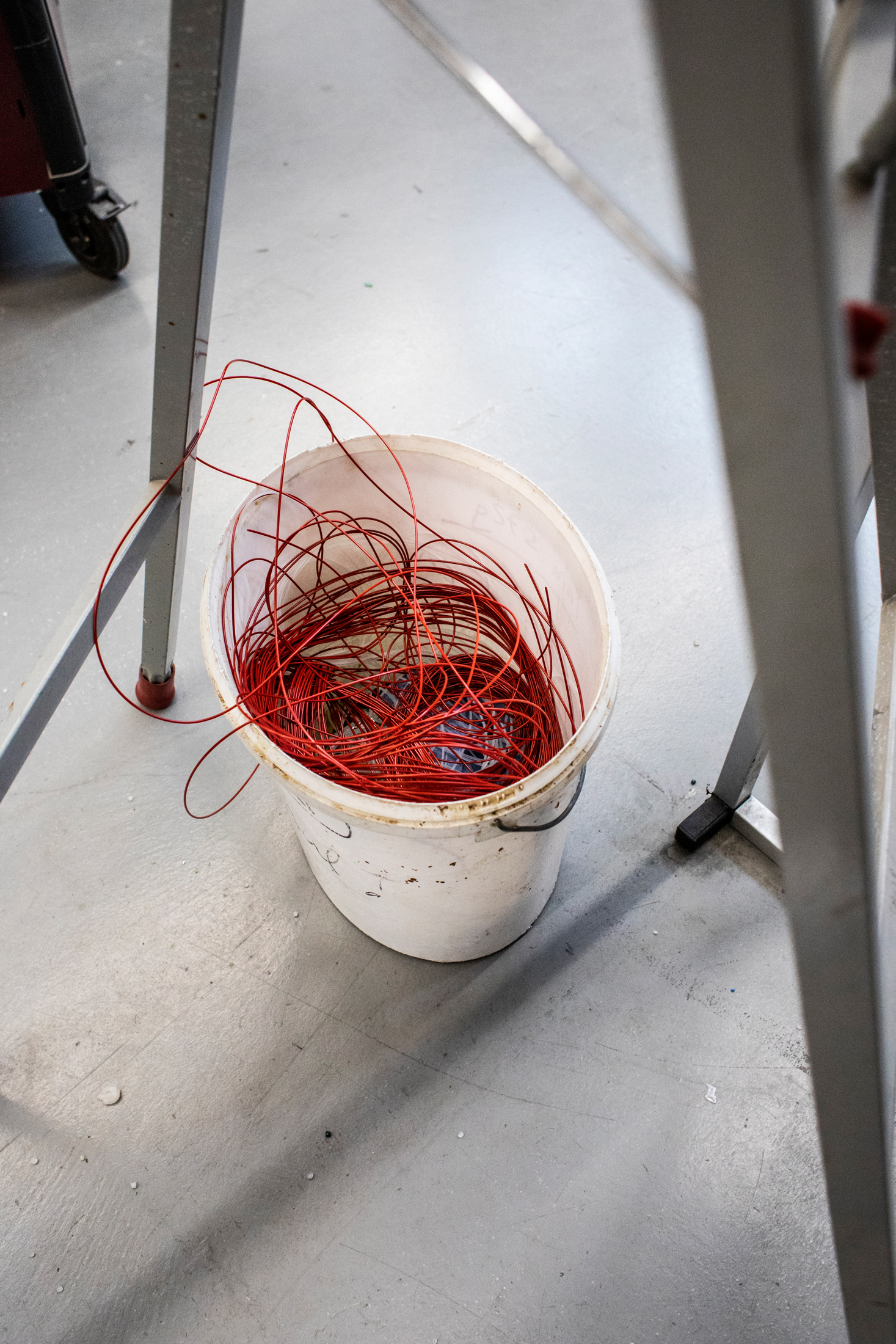
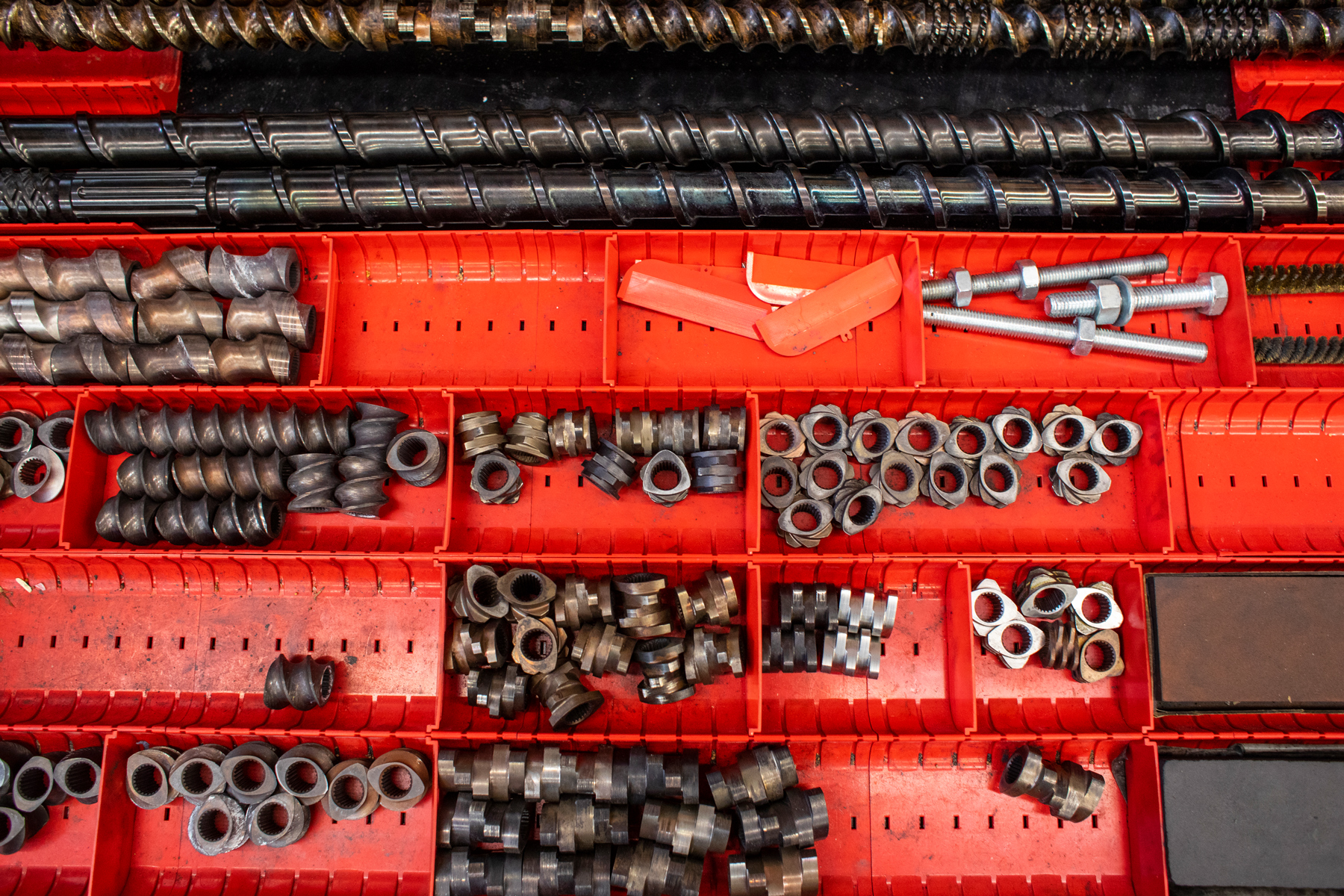
Alltägliches aus dem 3D-Drucker?
Nicht selten stehen Upcycling-Verfahren für den 3D-Druck noch in ihren Anfängen oder haben oft noch symbolischen Charakter. Sie zeigen aber auf, was mit Kunststoffabfällen grundsätzlich alles möglich ist. Es lassen sich viel graue Energie und Ressourcen sparen, was ein wichtiger Schritt hin zur 2000-Watt-Gesellschaft bedeutet. Gleichzeitig sensibilisieren sie auch für die Thematik an sich und veranschaulichen die Idee der Kreislaufwirtschaft. Damit sich der Ansatz aber im grösseren Stil durchsetzt, dafür braucht es mehr. «Eine grosse Herausforderung beim Kunststoff ist, dass neuer heute oft noch günstiger als recycelter ist. Gerade auch darum ist es wichtig, dass sich Upcycling-Produkte künftig auch am Markt behaupten können», so Schwendemann. In einer Kreislaufwirtschaft läge eine Symbiose beider Ansätze durchaus auf der Hand.
Eine Welt, in der man sich zu Hause ausdrucken kann, was man für den täglichen Gebrauch benötigt, ist in Zukunft grundsätzlich denkbar. Waren und Produkte müssten dann nicht mehr über Tausende von Kilometern hinweg transportiert werden, wodurch sich enorme Mengen an Treibhausgasen und Energie sparen liesse und Lager würden tendenziell überflüssig. Woher dann aber die Rohstoffe dafür kommen und auch welcher sich für welche Anwendung besonders gut eignet, werden dabei entscheidenden Fragen sein.
Trotz ihres Potenzials beim Einsatz für die Kreislaufwirtschaft fehlen zurzeit noch die gesetzlichen Grundlagen, die den Umgang mit der Technologie regeln und auch vor Missbrauch schützen.